Pattern Shop
- Home
- Pattern Shop
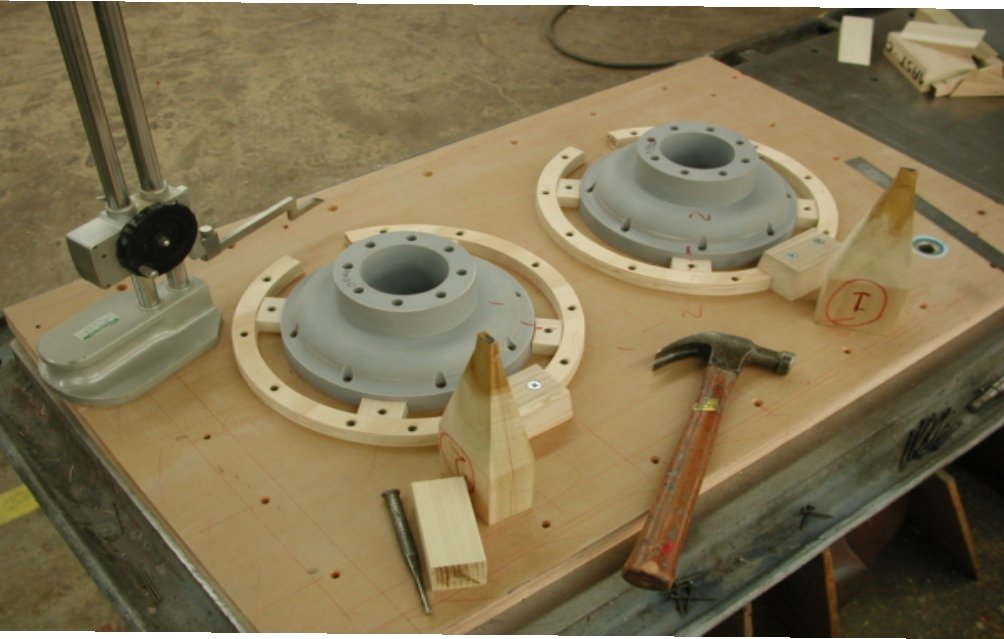
Despite the fact that we do not design products, we are still looking for ways to influence casting design and thus make the transition from concept to production easier. When CAD models are available, we are familiar with most modelling tools and make full use of it.
Within a few weeks of receiving an order, we manufacture prototype wooden and resin equipment (often using rapid prototyping) and first-off castings.
When the original patterns are not available, we often replicate castings using sample casting, which saves money and shortens lead times.
Our pattern makers have a wealth of experience with the Company and a wealth of expertise adhering to high standards of precision and tolerance, which necessitates a detailed understanding of foundry processes and technology.
We are committed to fulfilling your exact specifications, whether your castings are simple or complicated, require high volume or low volume use.
To achieve your desired result, our team of patternmakers, engineers, and foundry staff collaborate.
Traditional tooling methods can be the best option in some cases.
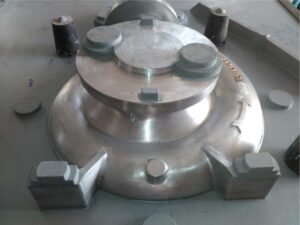
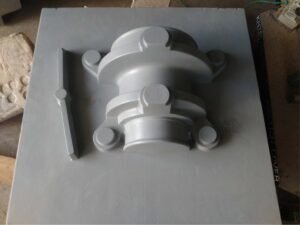

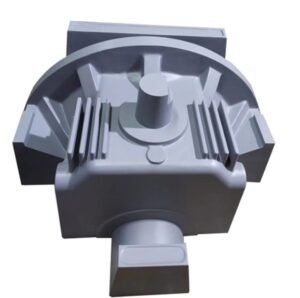
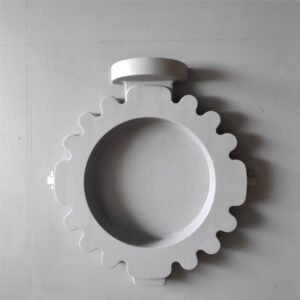